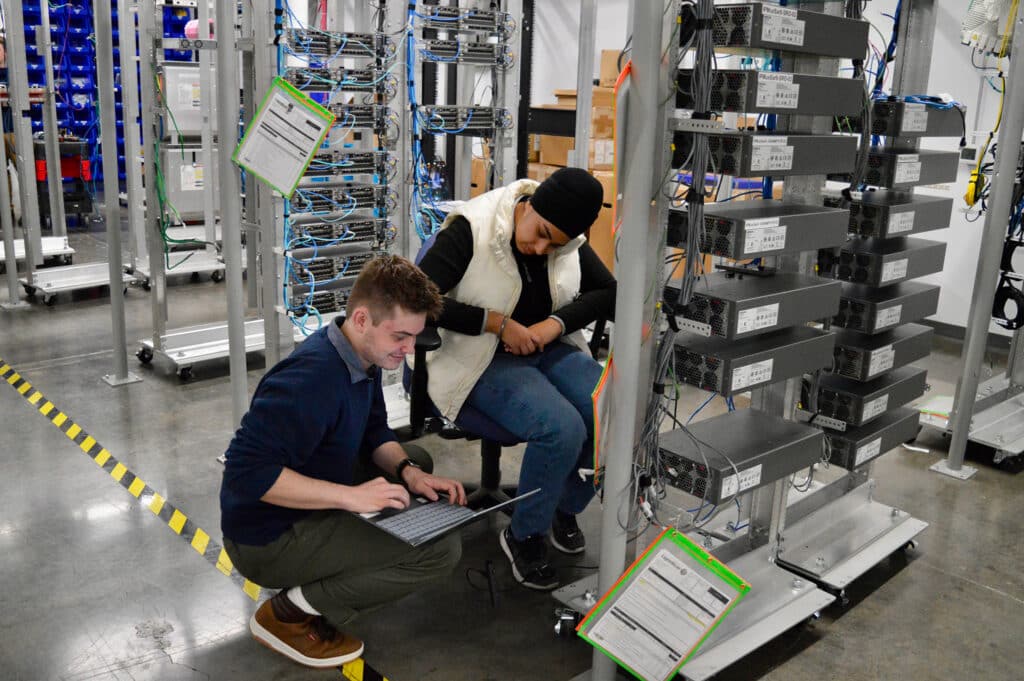
Factory Built Network ®
A patented process for building and deploying complex networks swiftly and predictably
How it works
Leverage our engineering expertise, vendor reach, testing facilities, and multi-vendor automation to deliver higher value networks faster
In combination with our unique multi-vendor technology laboratories and purpose-built network factories, LightRiver specialists build, deploy and support the highest-performing, most reliable transport networks with unprecedented speed and cost-efficiency. After an unparalleled battery of extended testing and burn-in in LightRiver’s facility, networks are deployed rapidly and efficiently in the field, completing new network deployment in record time, while offering an objective prescription for ongoing network health.
Single-source
Single vendor from start to finish accelerates outcomes and improves quality.
In-house
Work performed in-house for better control, improved quality & faster speed.
Global
Equipment is custom-crafted and shipped worldwide.
Reliable
Networks staged, configured, and burned-in at our Factory to prevent issues when deployed
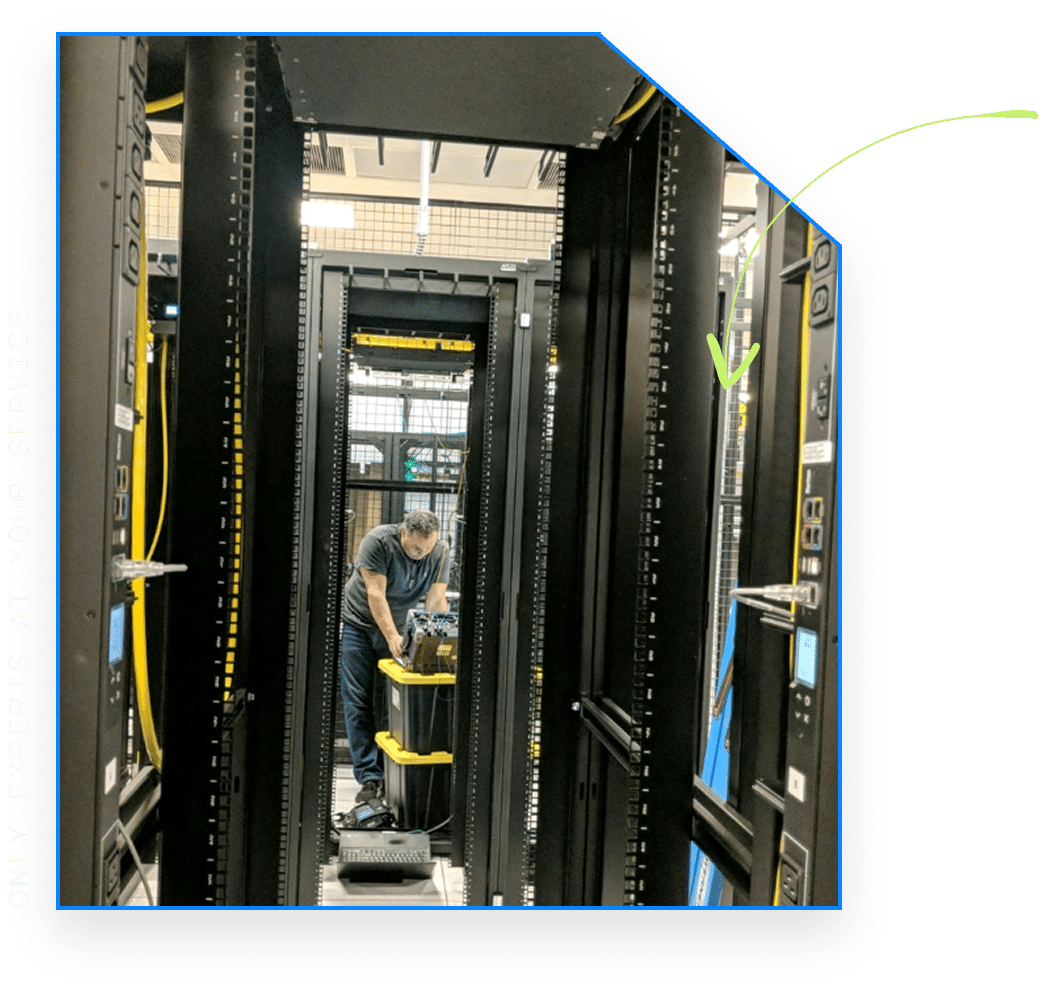
Why Factory Built Network?
Faster deployments, better results
- Vendor agnostic design, integration, and delivery to meet your business needs
- Over 60% less time onsite, including half as many site visits
- 8x more auditing & testing to provide a better performing network
- 94% of quality defects detected during factory testing
- Team empowerment via hands on network training
- Predictable installation schedules
- 50% faster project timelines
- Network monitoring to assure your services are delivered to customers as intended; all contributing to
- 65% reduction in customer staff requirements and associated cost to deploy a new network
Factory Built network Insights
Expertise for every step of your journey
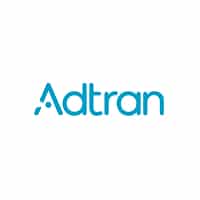
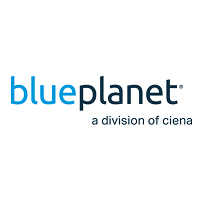
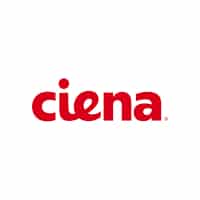
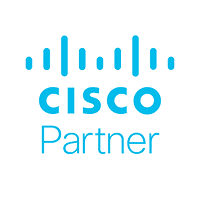
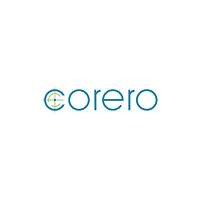
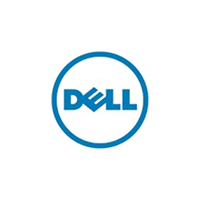
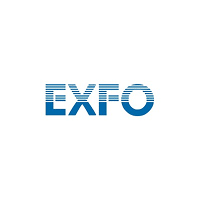
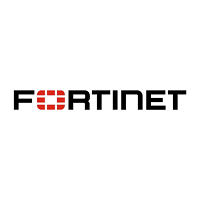
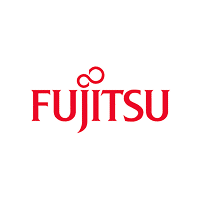
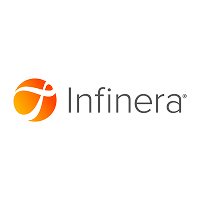
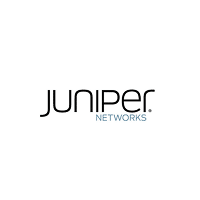
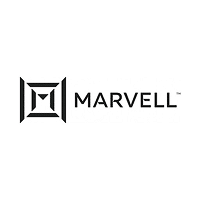
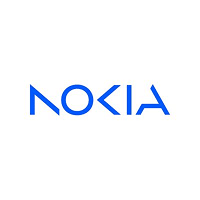
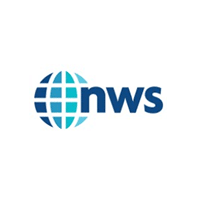
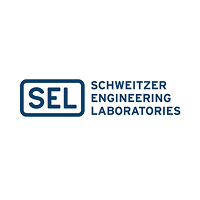
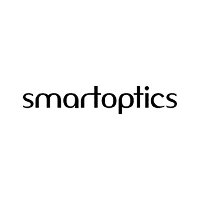